How to react more quickly to an urgent need for parts. Can 3D printing help? A comparison with injection molding.
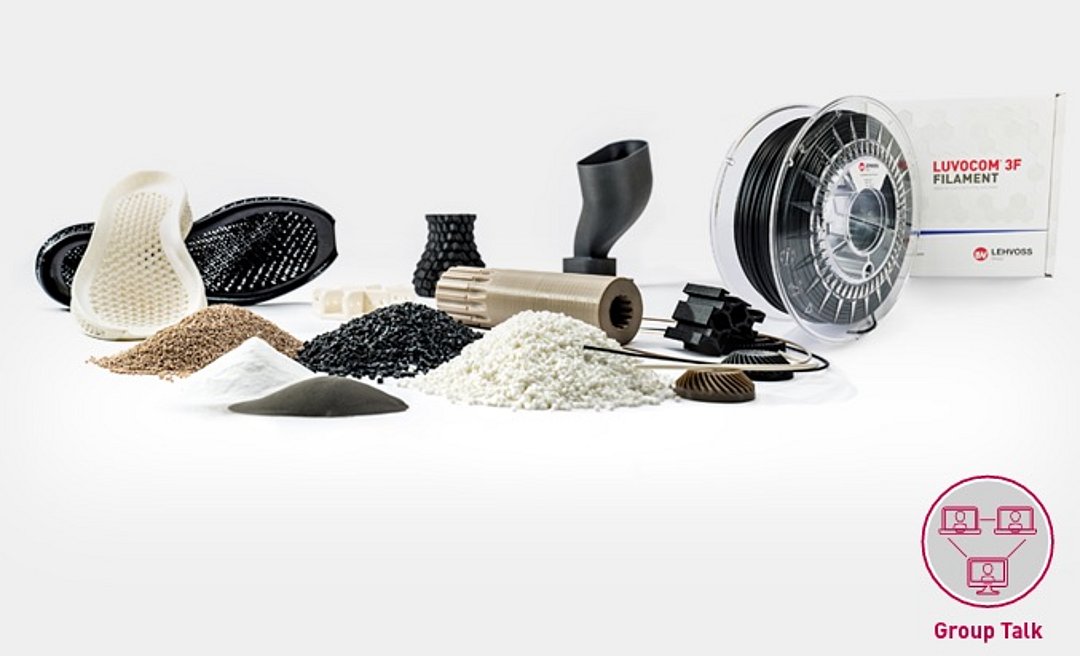
The current COVID-19 crisis shows the limits of global supply chains: Urgently needed parts are just not available. But 3-D printing along with tens of thousands of locally available (desktop) printers are currently helping to overcome shortages for such protective equipment as goggles and masks. Regardless of the production technology involved, all parts have to fulfill certain requirements: They need to be safe and functional over their lifetimes. And this requirement not only applies to the medical market, it also extends to all other industries like automotive and machinery.
Our 3-D Printing Materials team welcomes the opportunity to show you what 3-D printing materials can deliver in terms of mechanical performance and how this compares with injection molding. The team is also ready to discuss which materials are available now and how we can help you take advantage of this technology.
Thomas Collet
Thomas Collet heads the 3-D Printing Materials and Marketing departments in the business unit Customized Polymer Materials. He holds an engineering degree in polymer technology and has more than 32 years of experience in the polymer industry, 20 of them with LEHVOSS. He loves polymers because they always involve new applications, technologies and challenges.
His primary responsibilities today involve establishing 3-D printing as a technology for producing serial parts.
Dr. Thiago Medeiros Araujo
Thiago Medeiros Araujo studied materials engineering in Florianopolis, Brazil, completing his PhD in Trento, Italy, in materials science and engineering with a focus on polymer composites.
His first contact with additive manufacturing was producing novel filaments using bio-based materials, after which he joined Airbus Group Innovations where he was responsible for the low technology readiness level additive manufacturing processes.
Today Thiago is responsible for market development of LUVOCOM® 3F, the product line for extrusion-based processes in the 3-D Printing Materials Business team of LEHVOSS Group, located in Hamburg, Germany.
Dr. Marcus Rechberger
Marcus Rechberger is responsible for the global marketing of LUVOSINT materials for powder-based fusion processes like laser sintering as well as for electrostatic powder coating materials. An expert for particle technology and for bringing innovative products onto the market, he has 20 years of experience in 3-D printing and 3-D printing materials and holds a PhD and a degree in civil engineering.
Marcus enjoys being involved in customers’ projects from the very beginning when the focus is on new technologies or applications as he can provide added value here. What he likes the most about his work is to see products going live after the challenging period of working on them.
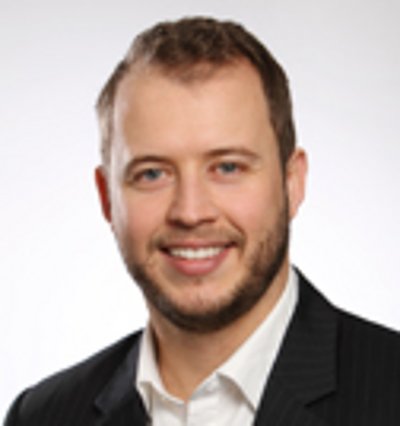
Market Development LUVOCOM® 3F
Dr. Thiago Medeiros Araujo
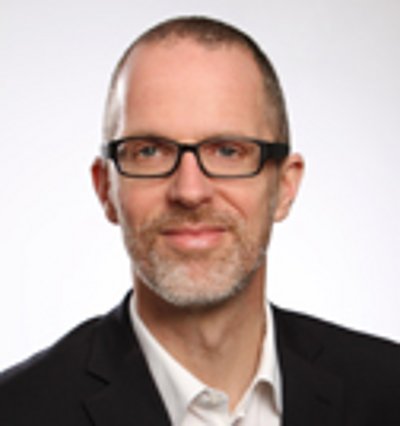
Market Development LUVOSINT®
Dr. Marcus Rechberger
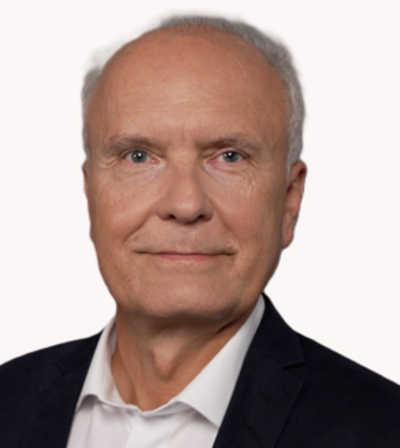
Director Marketing / Senior Sales Manager